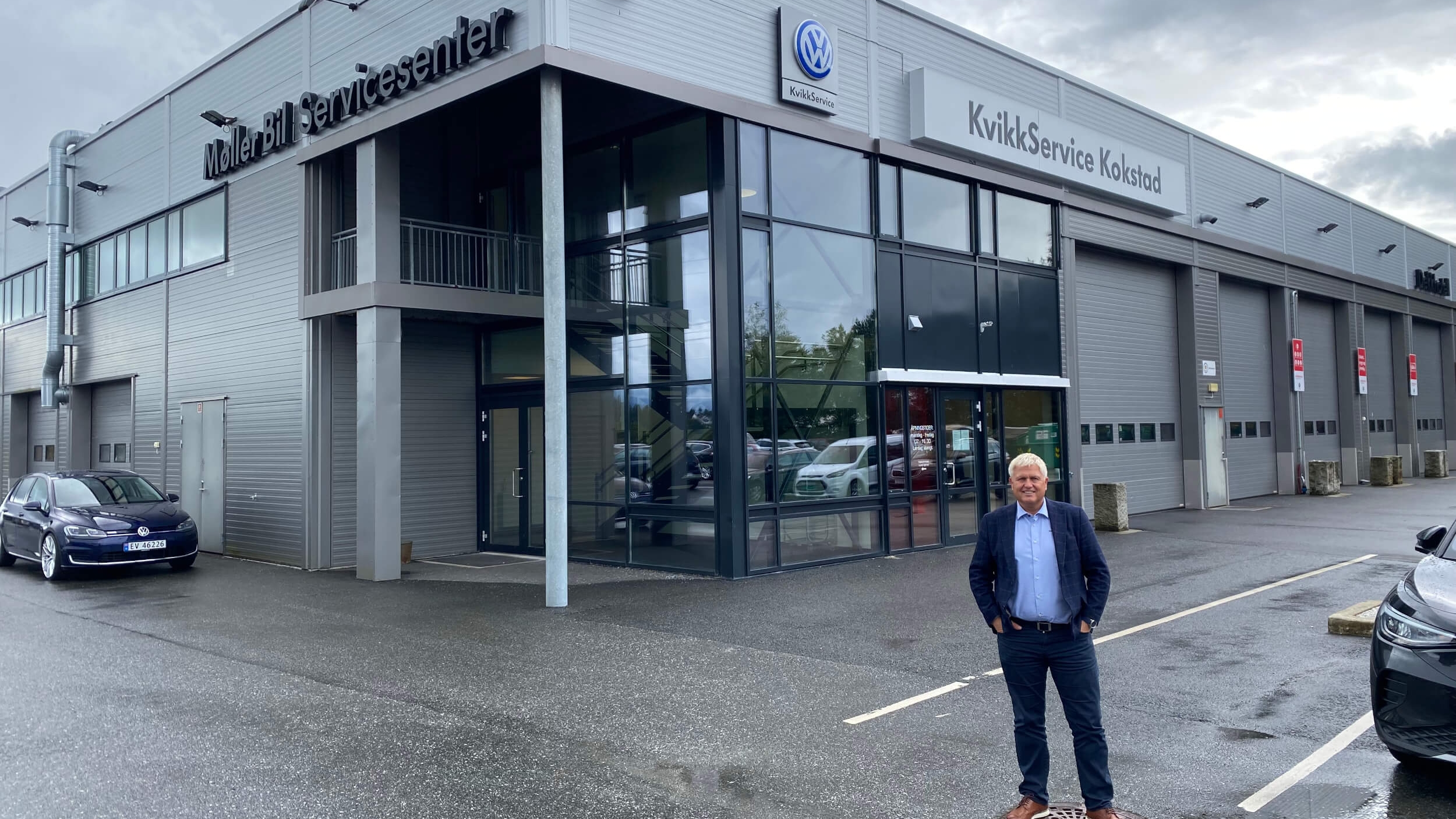
Kurt Eskevik, leder for skade i Møller Bil, er veldig fornøyd med resultatet på Kokstad, og ser frem til å ta i bruk samme konsept flere steder.
Det nye småskadeanlegget i Bergen som nylig åpnet tar i bruk ny teknologi og prosesser som både minsker fotavtrykket og sørger for bedre økonomisk drift. Dette er fremtidens konsept som skal rulles ut på alle nye skadeanlegg som bygges, samtidig som alle Møller Bils eksisterende skadeanlegg skal optimaliseres.
12. mai mai hadde Møller Bil offisiell åpning av sitt nye småskadesenter på Kokstad i Bergen. Dette er ikke bare et nytt småskadesenter – det er også et helt nytt konsept som heter «Sveno Zero» med spesielt fokus på å utbedre mindre skader. Målet for reparasjonstiden er imponerende én dag fra bilen kommer inn til den skal leveres ut igjen.
Det skal skje gjennom utstrakt bruk av raske produkter, nye tørkemetoder ved lakkering og fyring med elektrisitet, og uten ledetider eller stopp i produksjonsløpet. For å oppnå dette er anlegget bemannet med erfarent Møller-personell, de fleste med doble fagbrev innen oppretting, lakkering og/eller mekanisk.
Dette skal naturligvis sørge for at skadesenteret kan håndtere et høyt volum av biler, og dermed øke omsetningen og lønnsomheten.
Samtidig har et annet aspekt hatt like mye fokus under planleggingen og realiseringen av det nye skadesenteret: Nemlig å skape en mer bærekraftig reparasjonsprosess gjennom å redusere energiforbruket og det miljømessige fotavtrykket.
- Kokstad er bare startskuddet. Vi er helt sikre på at vi har funnet den rette løsningen på Kokstad for å både drive mer lønnsomt og samtidig mer miljøvennlig, sier Kurt Eskevik, leder for skade i Møller Bil.
Møller Bil har bærekraft som en sentral del av sin strategi, og gjør med disse investeringene alvor av å redusere sitt miljømessige fotavtrykk.
- Dette legger ytterligere press på utdaterte og forurensende lakkeringsanlegg i bilbransjen. Vi tar bærekraft på alvor, og disse nye løsningene som vi har kommet frem til sammen med Bolest setter en ny standard. Derfor er dette ikke noe vi vil holde for oss selv, men dele med resten av bransjen, sier Eskevik.
Gumpen Gruppen har allerede fått tilgang til samme konsept i sitt nye anlegg som de bygger i Kristiansand i samarbeid med Bolest.
Det nye skadeanlegget som bygges i Møller Medvind Arena vil være bygget etter samme konsept som på Kokstad, og det samme er tilfellet for alle fremtidige nybygg.
- Samtidig jobber vi med å optimere alle våre eksisterende anlegg, forteller Eskevik.
Et flertall av reparasjonene ved det nye anlegget på Kokstad vil være på brukte biler som kommer fra egne salgsavdelinger i regionen – blant annet bruktbilsenteret som ligger på samme tomt.
Kurt Eskevik, leder for skade i Møller Bil, er veldig fornøyd med resultatet på Kokstad, og ser frem til å ta i bruk samme konsept flere steder.
I prosjektets innledende fase
med ett mål for øye: Å skape en mer bærekraftig reparasjonsprosess for bilskader gjennom å redusere energiforbruk og det miljømessige fotavtrykket.
Etter en helhetlig vurdering av alle prosessene i et reparasjonsløp, ble lakkeringsprosessen definert som den fremste faktoren for å oppnå en mer bærekraftig reparasjonsprosess. En annen viktig forutsetning for prosjektet var at dette skulle gjøres uten negative økonomiske konsekvenser og uten å påvirke operatørenes hverdag negativt.
Selv om Møller Bil for lengst har fornyet sine anlegg og ikke lenger eier eller driver oljefyrte lakkeringsanlegg, er det fortsatt mange aktører som reparerer mye bil i gamle lakkeringsanlegg. Flere av disse driftes på oljefyring og mange er helt uten varmegjenvinning eller andre, moderne energisparefunksjoner.
I en typisk lakkeringsprosess benyttes det kun én kabin for både lakkering og tørking, en såkalt kombikabin. I en kombikabin sprøytes objektene med en temperatur på omkring 22 grader. Deretter skal kabinen raskest mulig varmes opp til et sted mellom 60-80 grader for tørking. Denne temperaturen opprettholdes kun i noen minutter. Kabinen tømmes så raskest mulig for all den oppvarmede luften. Dette er en svært energikrevende prosess, med stort potensiale for både miljømessig og økonomisk besparelser.
I samarbeid med Bolest ble det derfor definert to sentrale spørsmål for prosjektet:
Løsningen ble å gå vekk fra gass som energibærer til fordel for elektrisitet. I tillegg ble den fysiske prosessen for henholdsvis lakkering og tørking separert.
I denne nye løsningen neddimensjoneres effekten i sprøytekabinen fordi de raske temperaturhevingene som kreves i en kombikabin er flyttet til eget rom. I tillegg tilpasses effekten og luftmengden avhengig av størrelsen på jobben som skal lakkeres.
Lakkeringskabinen leveres med meget effektive varmegjenvinnere, med minimum 70 prosent virkningsgrad. For å sikre full effekt av disse i hele anleggets levetid er de satt opp med automatisk rengjøring.
I den separate tørkekabinen varmes luften opp kun en gang om dagen og bruker i all hovedsak resirkulerende luft, fremfor å varme opp for så å «kaste» den oppvarmede luften flere ganger om dagen. I løpet av en driftsdag vil kun 5-10 prosent av luften byttes ut gjennom en effektiv varmegjenvinner.
Og besparelsene er imponerende. Beregninger gjort av en gjennomsnittlig skadejobb utført ved normale temperaturer gir følgende resultater*:
- Selv om vi altså øker antallet skadejobber, vil vi ikke øke vårt fotavtrykk nevneverdig. Dette er dermed bærekraftig i dobbel forstand, sier Eskevik.
- Bolest er mer en partner enn en leverandør, og vi er veldig fornøyd og takknemlig for jobben de har lagt ned sammen med oss, legger skadesjefen i Møller Bil til.
Asgeir Elvstedt er administrerende direktør i Bolest, og legger ikke skjul på at også er svært fornøyd med både prosessen og resultatet:
- Vi har samarbeidet tett med Møller Bil om dette konseptet frem til nå, og er imponerte over hvor stor besparelsen er ved å benytte denne metoden. På lik linje med Møller Bil er bærekraft noe vi har høyt på agendaen, og vi ser frem til å ta «Sveno Zero»-konseptet ut til flere aktører i bransjen, sier Elvstedt.
* Tallene bygger på årsmiddeltemperatur i Bergen 7,8°C, sprøytetemperatur 22°C, tørketemperatur 60°C. 7 driftstimer med 6 skader daglig i kombikabinen, 7 driftstimer og 12 skader daglig i løsningen med separat sprøyte og tørkekabin. Kabiner med energispar er kalkulert til å gå 10 % av driftstid i sparemodus. Skademiks for ny løsning 10 % SMARTrepair, 75 % småskader, 5 % store skader.
Sist oppdatert - 21. januar 2025Trenger du en leiebil? Møller Bil og Hyre gir deg nå enkel tilgang til små og store biler for enhver anledning.
Med lidenskap for bilfag og solid støtte fra Møller Bil gikk Simen Totland Bergsholm fra lærling til deltaker i World Skills 2024, populært kalt yrkes-VM. Der fikk han måle sine ferdigheter mot verdens beste unge mekanikere.
Vi har åpnet dørene på det nye senteret for nyttekjøretøy hos Møller Bil Hvam utenfor Oslo. Med et dyktig lag på firmabil, ny butikk og oppgradert verksted skal de tilby et komplett servicetilbud til bedriftskunder.